The heat duct transition piece was cut at a 45 deg angle on the square end.
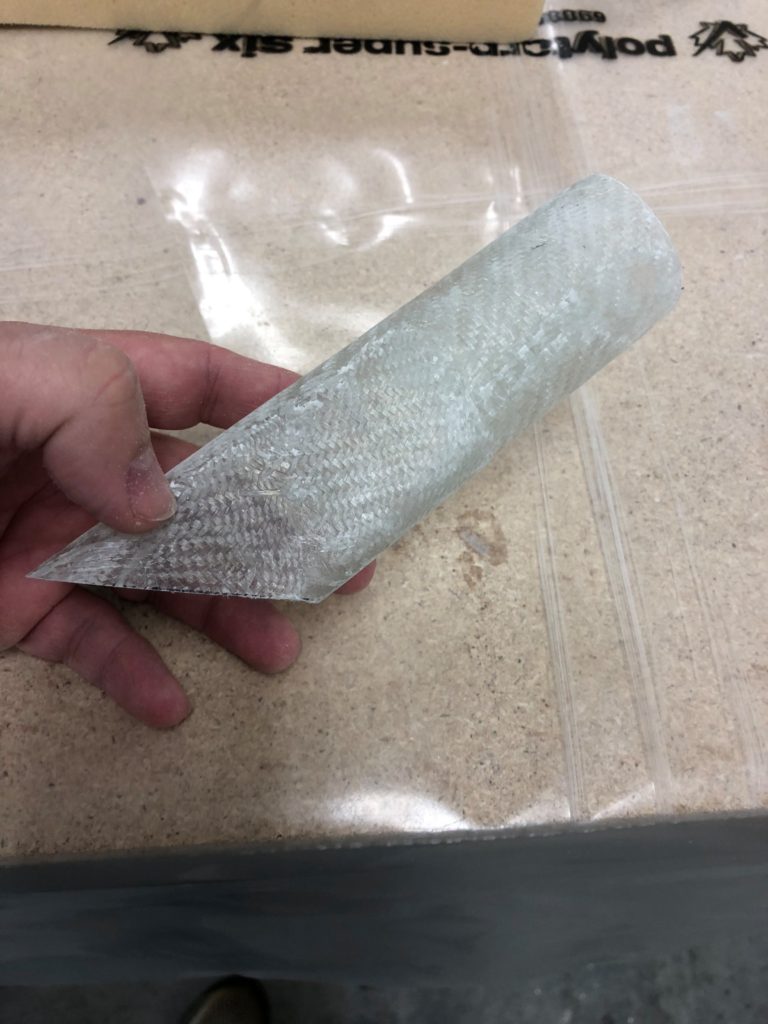
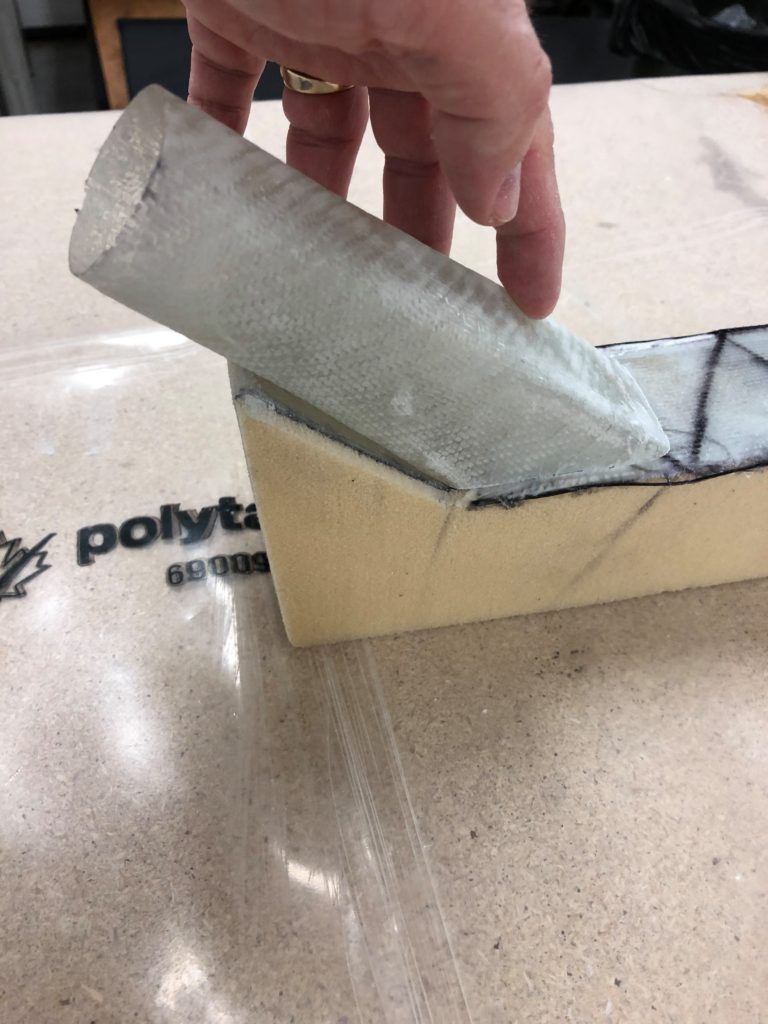
The 1″ hole under the left side longeron was re-opened using an electric drill.
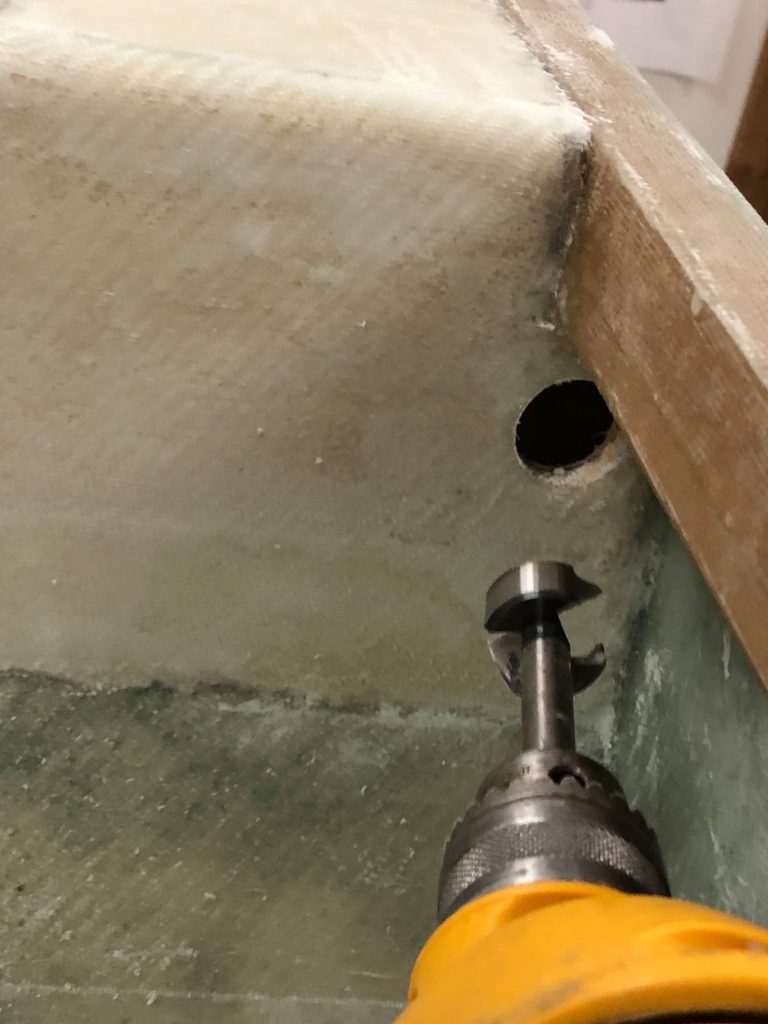
The back edges of the seatback were trimmed and sanded. The peel ply was removed from the front side of the seatback.
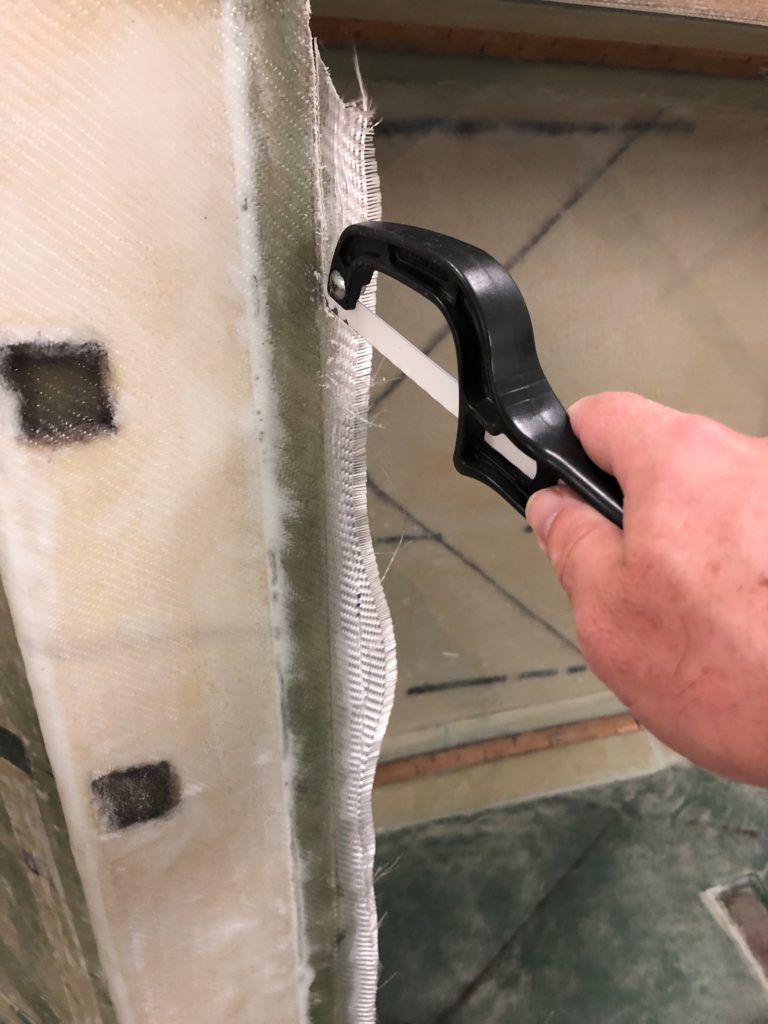
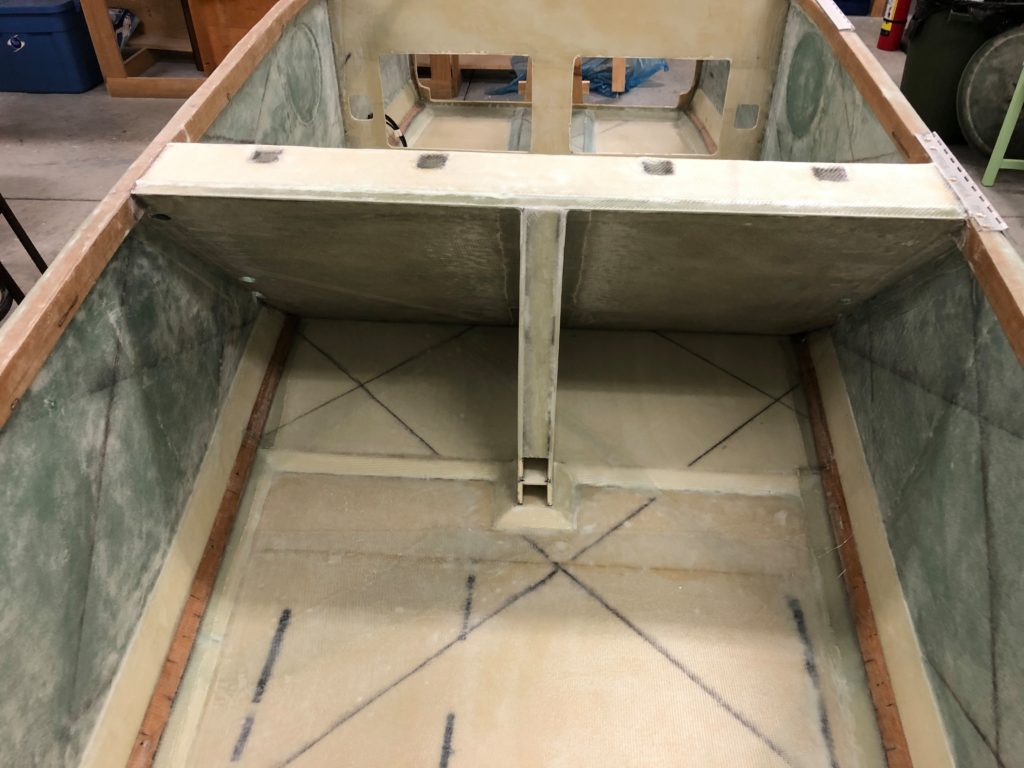
3-ply of UND cloth was cut 4″ wide by 13″ long for each of the four harness attachment points.
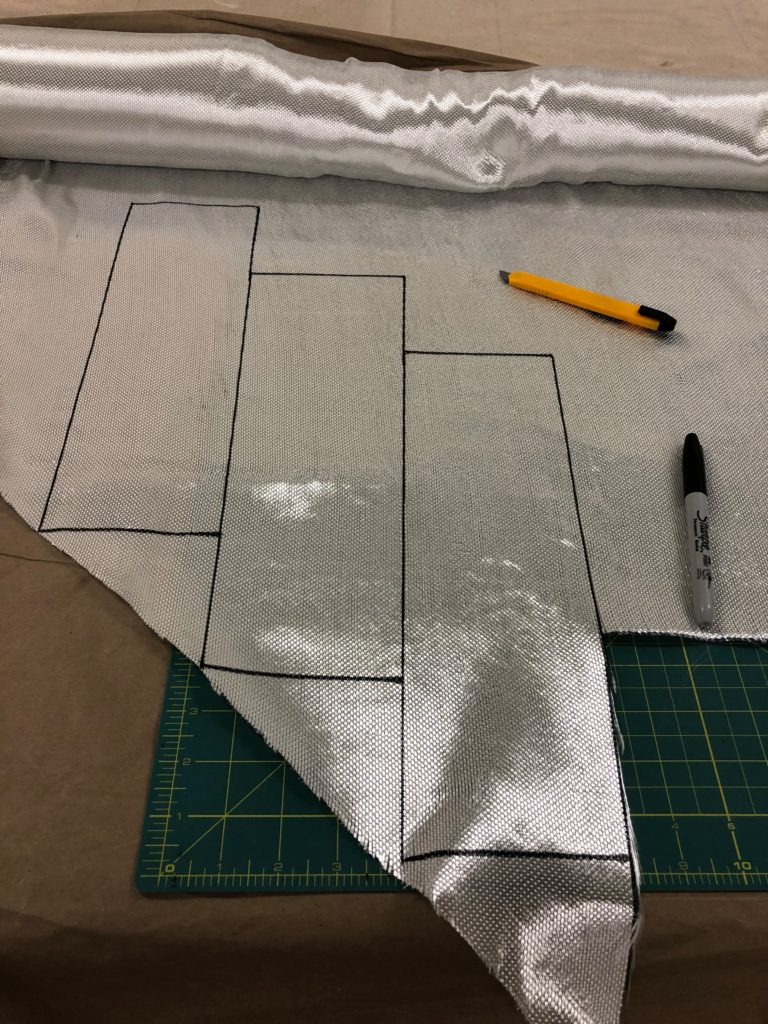
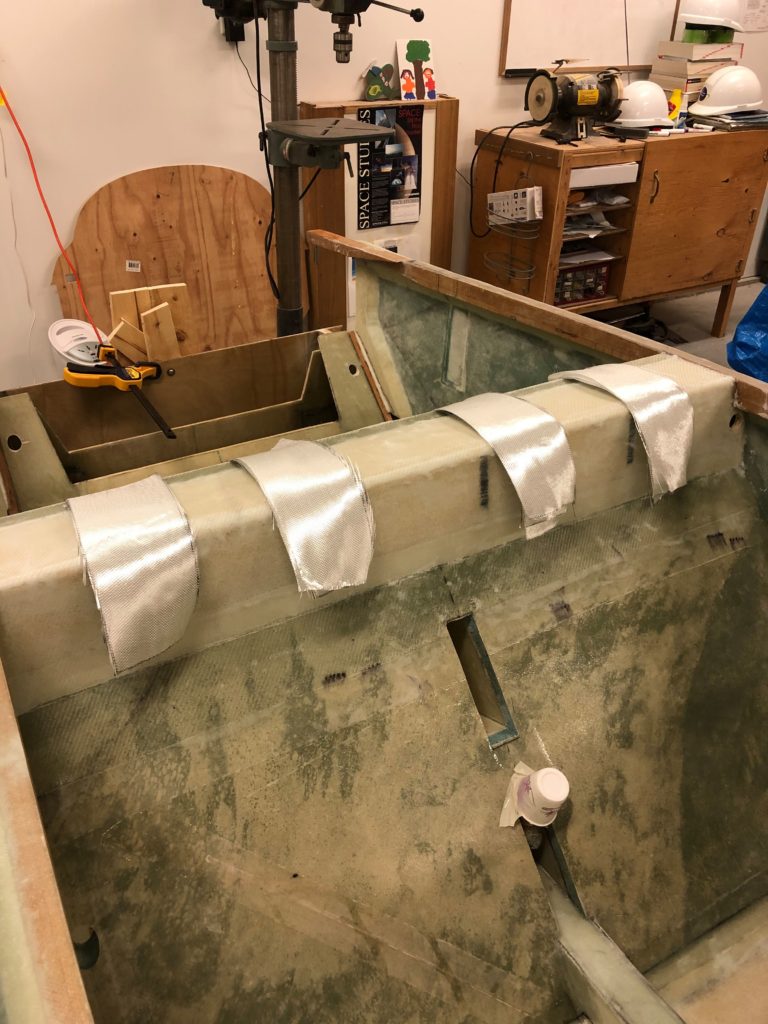
With the workshop temperature at 24deg C and humidity 58%, a batch of epoxy was mixed using116g resin and 44g hardner. The epoxy was used to lay up the 3-ply UND on each of the harness attachment points such that they ran from 2″ below the shoulder support at the front all the way to the back of the seatback at the top.
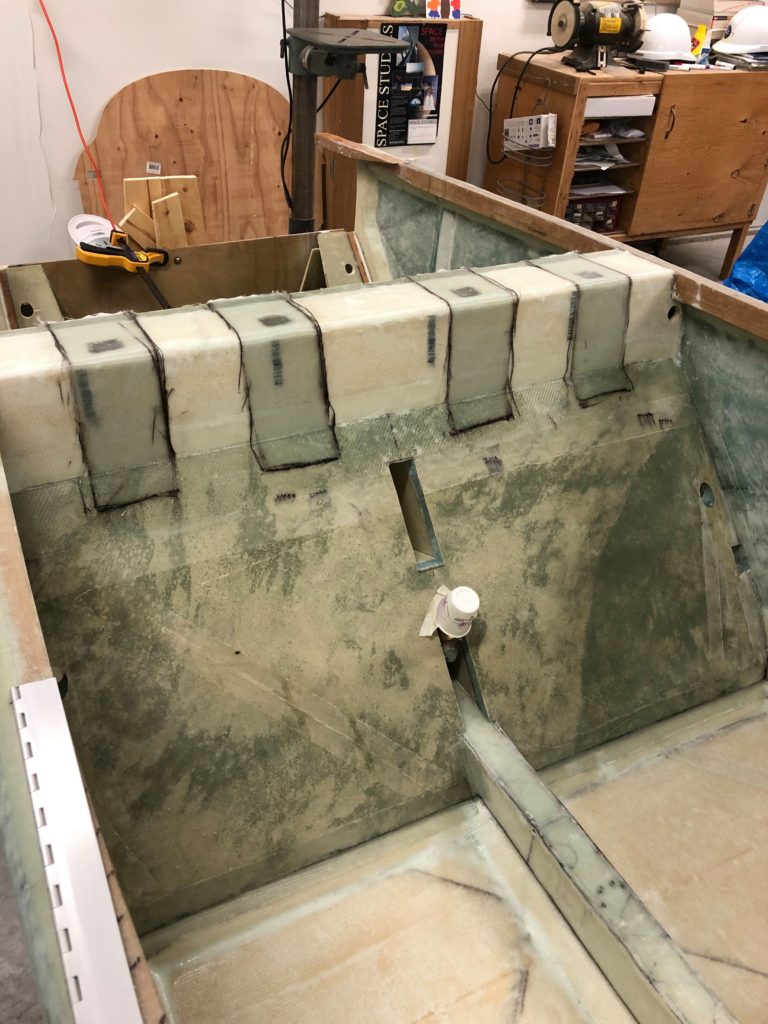
